Using OpenSCAD to build custom 3D pieces Build Your Own Body
Tutorials – OpenSCAD
OpenSCAD lets you use simple scripts to build 3D bodies from primitive shapes that you can then send to your 3D printer. It also lets you create custom shapes for pieces and objects. In this article, we look at two ways to do just that.
In last month's installment [1], you saw how to use primitive 3D bodies (cubes, spheres, cylinders, etc.) to build complex 3D objects. Apart from combining basic primitives, there are more ways of making bodies in OpenSCAD [2]. One is to extrude them from 2D shapes; another is to build them from a bunch of vertices and faces you define in arrays.
Let's see how both of these work by building an "arm" that will let you attach a sports camera to a printer's hotbed. This arm could look something like what you can see in Figure 1. With the arm attached to the bed, you will be able to monitor your print with the action always in the center of the frame.
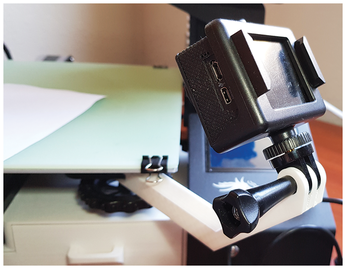
[...]
Buy this article as PDF
(incl. VAT)
Buy Linux Magazine
Subscribe to our Linux Newsletters
Find Linux and Open Source Jobs
Subscribe to our ADMIN Newsletters
Support Our Work
Linux Magazine content is made possible with support from readers like you. Please consider contributing when you’ve found an article to be beneficial.
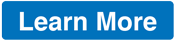
News
-
Happy Birthday, Linux
On August 25, Linux officially turns 34.
-
VirtualBox 7.2 Has Arrived
With early support for Linux kernel 6.17 and other new additions, VirtualBox 7.2 is a must-update for users.
-
Linux Mint 22.2 Beta Available for Testing
Some interesting new additions and improvements are coming to Linux Mint. Check out the Linux Mint 22.2 Beta to give it a test run.
-
Debian 13.0 Officially Released
After two years of development, the latest iteration of Debian is now available with plenty of under-the-hood improvements.
-
Upcoming Changes for MXLinux
MXLinux 25 has plenty in store to please all types of users.
-
A New Linux AI Assistant in Town
Newelle, a Linux AI assistant, works with different LLMs and includes document parsing and profiles.
-
Linux Kernel 6.16 Released with Minor Fixes
The latest Linux kernel doesn't really include any big-ticket features, just a lot of lines of code.
-
EU Sovereign Tech Fund Gains Traction
OpenForum Europe recently released a report regarding a sovereign tech fund with backing from several significant entities.
-
FreeBSD Promises a Full Desktop Installer
FreeBSD has lacked an option to include a full desktop environment during installation.
-
Linux Hits an Important Milestone
If you pay attention to the news in the Linux-sphere, you've probably heard that the open source operating system recently crashed through a ceiling no one thought possible.