Get creative with the FLUX Beamo laser and open source software
Beam Me Up, Fluxy!
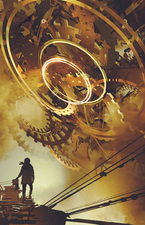
© Lead Image © Tithi Luadthong, 123RF.com
With the FLUX Beamo laser and a Raspberry Pi Board B10001, you can execute your own laser cutting projects on a wide range of materials.
Laser cutting mainly used to be the purview of hard-headed business owners with solid financial backing and a business plan to make sure the laser paid for its upkeep. And there were hobbyists who were more interested in the arts and crafts side of laser cutting and saw the laser as a tool for cutting and engraving materials such as wood, cloth, and acrylics in the scope of their arts and crafts projects. The trouble was, many people were more than a little worried about the Heath Robinson-style, low-budget lasers they could purchase at the time. The foundations of the laser world were to be shaken though, when FLUX – an organization founded by a "group of passionate young engineers and designers," as the manufacturer itself states – launched the Beambox laser cutting machine back in 2018. FLUX quickly followed up with the Beamo, promoted as "the world's smallest laser cutting machine" the next year.
The FLUX laser family not only meant a paradigm shift in terms of laser cutting machine pricing, but also a move towards a community-driven approach. For one thing, the FLUX laser family relies on a Raspberry Pi, in the form of the Raspberry Pi Board B10001 [1], to control the machine. And the downloadable software package that lets users send their ideas (in the form of, say, PNG images or vector diagrams) to the laser runs on your choice of operating system, whether this be Windows, macOS, or Linux. Expanding on the community idea, FLUX users can get together to exchange ideas on Facebook or at regular FLUX community meetings that take place all over the world – even in Germany, where we're based. So, laser-affine readers, let's get started with unboxing and the setup on the hardware and software side.
Unboxing
The FLUX Beamo reaches its new owner in a very large and fairly heavy cardboard box. If you are worried about the state of your back, then it's a good idea to ask a friend to help you lift the beast out of the box. Once you've done this, there are a couple of tasks to complete before you get started on your first project. Besides doing the obvious things like removing the vent hose and attaching it to the duct on rear of the laser with the clamp kindly provided by the supplier, attaching the WiFi antenna, and plugging in, there is also the software setup. This no big deal: After powering on your laser cutter, select Network on the Start screen (Figure 1) and then Connect to WiFi if you are using the machine's wireless interface. Choose a WiFi network, enter the password, and let DHCP do its magic. You can alternatively use the Ethernet cable provided – this can be a good idea if the WiFi connection is too slow or unreliable. Once the machine has an IP address, make a note of the address and move on to the next stage, installing Beam Studio.
[...]
Buy this article as PDF
(incl. VAT)
Buy Linux Magazine
Subscribe to our Linux Newsletters
Find Linux and Open Source Jobs
Subscribe to our ADMIN Newsletters
Support Our Work
Linux Magazine content is made possible with support from readers like you. Please consider contributing when you’ve found an article to be beneficial.
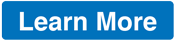
News
-
Fedora Continues 32-Bit Support
In a move that should come as a relief to some portions of the Linux community, Fedora will continue supporting 32-bit architecture.
-
Linux Kernel 6.17 Drops bcachefs
After a clash over some late fixes and disagreements between bcachefs's lead developer and Linus Torvalds, bachefs is out.
-
ONLYOFFICE v9 Embraces AI
Like nearly all office suites on the market (except LibreOffice), ONLYOFFICE has decided to go the AI route.
-
Two Local Privilege Escalation Flaws Discovered in Linux
Qualys researchers have discovered two local privilege escalation vulnerabilities that allow hackers to gain root privileges on major Linux distributions.
-
New TUXEDO InfinityBook Pro Powered by AMD Ryzen AI 300
The TUXEDO InfinityBook Pro 14 Gen10 offers serious power that is ready for your business, development, or entertainment needs.
-
Danish Ministry of Digital Affairs Transitions to Linux
Another major organization has decided to kick Microsoft Windows and Office to the curb in favor of Linux.
-
Linux Mint 20 Reaches EOL
With Linux Mint 20 at its end of life, the time has arrived to upgrade to Linux Mint 22.
-
TuxCare Announces Support for AlmaLinux 9.2
Thanks to TuxCare, AlmaLinux 9.2 (and soon version 9.6) now enjoys years of ongoing patching and compliance.
-
Go-Based Botnet Attacking IoT Devices
Using an SSH credential brute-force attack, the Go-based PumaBot is exploiting IoT devices everywhere.
-
Plasma 6.5 Promises Better Memory Optimization
With the stable Plasma 6.4 on the horizon, KDE has a few new tricks up its sleeve for Plasma 6.5.